
I'm not sure why I'm so surprised at the scale of this operation. You would expect a site that works seven days a week, 365 days a year, shipping thousands upon thousands of packages both domestically and globally to be on a significant scale - but DHL's operation at East Midlands Airport (EMA) is still breathtaking. I genuinely feel as if I have stumbled in to the set of a new James Bond set-piece.
But this is no fantasy-land, this is DHL's UK international hub at EMA, their largest hub in the UK and, with my watch showing 2130, their working day is just beginning.


"By the end of the night this place should be empty of packages," says our guide for the evening, Danny Pedri. Danny, DHL's Managing Director for Hubs and Gateways (UK and Ireland), has been with the company for 28 years and knows everything we need to know about the business. "This place" is the vast warehouse that is the centrepiece of DHL's operation at EMA - and the reason why I imagine Daniel Craig is about to come running past in a dinner jacket being chased by a bunch of heavies.
Having crossed the mid-way point of this vast building we are now 'airside' and have gone through all the processes you would expect such a move to entail; presentation of passports for the correct security authorisation, x-ray scanners for bags, coats, shoes and belts; frisking and further security checks before gathering ourselves together to head towards the heart of the hub itself.
Before having a good look round Danny gives us a run-down of the vital statistics, hopefully they will convey something of the scale I'm talking about.


"This site was opened in 2000 and is a purpose built 63 acre, £35 million hub. We operate from here every day, all year round and have 10,000m² of office accommodation and 30,000m² of warehouse with four kilometres of conveyor belts capable of handling 45,000 shipments an hour, or in other terms, 1,200 tonnes of material per night. There is 10,000m² of truck canopy and 35 truck bays along with parking for an additional 70 trucks and, of course, 18 aircraft parking stands which cover something like another 160,000m²."
It's pretty amazing stuff and all designed to ensure that DHL achieves one aim; that of delivering shipments to its customers in the time specified when they booked their pick-up.
Many thousands of UK businesses require fast, secure and reliable international express services, allowing them to operate effectively and compete in the global economy. Due to the distances involved these deadlines can very often only be met by aircraft, which means that DHL's East Midlands hub is actually playing a strategic role in supporting the UK's economy.


"The industry standard used to be an overnight service that customers would expect to arrive by close of business on the following day," explains Danny.
"What we are seeing now though is a shift for the entire industry and more and more customers are expecting delivery by lunchtime the following day. That will become the new industry standard."
One of the most extraordinary things about this huge operation is that most of the equipment which physically handles the shipments as they transfer between aircraft and truck is mechanical; not computerised or automated in any way. We will see and hear of some incredible technology as we are shown around this facility but central to its success is good old fashioned manual labour.
"We have a very loyal, hardworking and reliable team of staff here," says Danny.
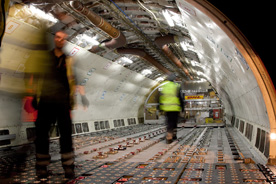

"They are the ones who make this tick and while we could install equipment that would take them out of the loop why would you? The core of our business is shipping 'widgets', small size but high value components such as computer chips, car parts and medical equipment, that kind of thing. But we do also see large shipments from time to time, it could be something like an aircraft engine or similar. We wouldn't be able to transfer that through an automated system anyway."
As we make our way across the huge expanse of warehouse we follow Danny up one level where the conveyor belts are rumbling away above our heads, while below us a group of staff are scanning packages once they have gone through the recently installed x-ray machines; a relatively new addition to satisfy recent changes to security regulations. The staff operating the machines are allowed to x-ray a maximum of 720 items per hour and, when this process is complete, the shipments are given their first 'sort' and divided up according to destination and deadline. There are hundreds of packages being dealt with as we look on.
"It's quiet at the moment," says Danny.
"At two or three o'clock in the morning, that's the time it gets really busy."


Incidentally, while some operations use dogs to sniff for explosives and other such illegal goods, technology using trained bees is also being developed to fulfil this vital role. The bees are trained to react to the smell of explosives and their tongues extend, breaking a control beam located in the container. Sounds unlikely? OK, we didn't believe it either but have a search on the web and you'll find that this unlikely partnership between bees and humans is indeed a reality, although one not employed by DHL.
You can't help but wonder how on earth they keep track of all of these packages, but that is one area where technology really does come in to play.
"Every shipment's delivery is preceded by its own packet of information. So the moment DHL collects a package for delivery it is scanned and present on our computer network; this has many benefits for both us and our customers. Firstly, our customers can track their shipments 'live' at all stages of the process so they can see exactly whereabouts it is at any time. Even ten or fifteen years ago we weren't really able to tell our customers too much about where their shipments were during the process, so this is hugely beneficial and gives them the confidence that their shipment won't go missing. If anything does go awry, and mistakes do happen from time to time, we are able to tell them exactly why and how we will rectify it - probably before they have even noticed that there is a problem. I think our customers appreciate that."


The second part of this information package is even more impressive.
"As soon as that data moves on ahead of the shipment it tells the destination to expect it and actually starts the customs clearance process, which can obviously save a lot of time on arrival. DHL has one of the only private connections in to the UK customs network and, as a trusted provider, we are able to clear customs very quickly and largely unhindered, as we are effectively working in partnership with customs."
Making our way to the far corner of the warehouse we follow Danny through a security controlled door and take a lift up to the top of the building where DHL has installed its own control tower. It's dark and quiet in here but as we move away from the escalator we see that the glass frontage offers a spectacular view across the DHL ramp. To our right is one of their new additions - a Boeing 767 ERF, quietly awaiting the frenzy of activity that will it see it loaded and prepared for its early morning trans-Atlantic departure. Immediately adjacent, an Airbus A300 is being prepared for a trip to Leipzig, DHL's largest European hub. A Boeing 757 and another Airbus are being readied away to our left while the distant end of the ramp sees a leased Boeing 737 and an ATP also awaiting their cargo.


Climbing a short flight of stairs we greet the four men who are manning the control tower, busy talking on the radios and monitoring the bank of screens that show them exactly what is due to happen through the night and exactly when it is supposed to happen. We are given a closer look and the screens, which update on a live basis, show arrival times, departure times, destinations, fuel uplift, cargo weight and also highlight any possible technical problems.
"They are talking to their colleagues downstairs and managing the flows dynamically and looking after capacity control, while also talking to the aircrews, the refuelling teams and the maintenance people."
Suffice to say, with such a dynamic business, decisions are taken on the night and they are decisions that can only be taken as a reaction to that evening's events. It's a highly pressurised situation.


"We have a Network Control Manager downstairs, who co-ordinates the nightly events in close co-ordination with the Ramp Manager and the Sort Manager. It is only by liaising closely with one another that they can make the decisions that keep everything running smoothly."
It is a remarkably complex business with something like 35% of the cargo that comes to EMA not of UK origin or for UK delivery. Cargo could, for example, be arriving from the USA and its destination could be Spain, or Scandinavia or well, pretty much anywhere really. If you think of any connection between countries or regions then it can probably happen via the DHL hub at EMA.
But, with so many hubs and spokes holding the network together, how much does it take for something to bring it all down? It seems to me that every part of the process is reliant on each hub getting through the night smoothly and with no dramas.
"It's much harder for that to happen than it used to be," admits Danny.

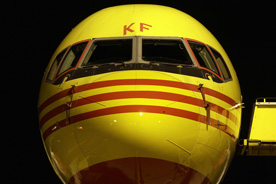
"Now that we have multi-hubs we can actually bypass any location. We still have a main European base (Leipzig) but we are now able to get to any hub in the network from any other part of the network. If EMA was out for any reason we could get to Spain via Brussels, or Italy via Leipzig for example. The problem would be localised so while the UK part of the business would be affected it wouldn't have a knock-on effect as we no longer have our eggs all in one basket."
Every foreseeable disruption is taken in to account Danny explains. A poor weather forecast, Bergamo is notorious for fog as an example, will see the aircraft with the latest avionics used to enable them to get in despite the weather. Industrial action would see aircraft flown in to an adjacent country and then trucks used to move shipments and so on. I can't emphasise enough just how impressive this display of logistical nous is - dynamic, flexible and the result of experience and teamwork.
That teamwork is very much in evidence when we venture out on to the floodlit ramp to see the aircraft more closely. Turn-around times are incredibly short and most depart some 60 minutes or so after arrival, having been unloaded and, of course, subsequently reloaded; while for the larger members of the DHL fleet such as the 767 and 777 (the 777s are actually operated through a joint-venture with Lufthansa Cargo) the timings involved are very slightly longer but no less impressive.

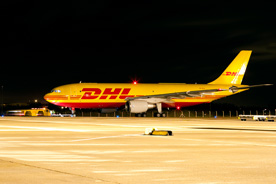
I've never been in an airliner in cargo-fit before and it's slightly disconcerting to see not only the network of pipes and wiring clearly visible in the ceiling of the cabin but also because, without seats or lockers and such like, it looks absolutely vast. A team of four are busy loading the Airbus, for that is what we are standing in, with the large containers being lifted hydraulically and then physically pushed along with cabin to their correct location.
The entire floor is covered in small free rolling balls which enable the containers to move freely, helped of course by some elbow grease from the team. Weight distribution is naturally of vital importance for safety and also fuel economy with each container marked to ensure it is loaded in to the correct section of the cabin, while each also comes with paperwork which, when scanned, instantly reveals details of every single shipment it contains.
In the time we spend outside on the ramp we see three aircraft loaded to capacity and then depart onwards for their next destinations and it occurs to me that this has probably been one of the most fascinating visits any of us have made since GAR's formation. By the time we gather to say thank you and farewell to Danny, guided tour over, it is almost midnight. But for the five hundred or so workers who remain, their night is just beginning however, their busiest time is still to come. By 6am they will have cleared that huge warehouse of shipments and played their part in keeping an incredibly complex network running smoothly so that later that day, thousands of customers who rely on DHL will take delivery of their important packages.



If you would like to discuss using any of our imagery or feature content please contact us.